Geocomposite drain is advanced geosynthetic drainage solutions designed to replace traditional granular layers in civil and environmental engineering projects. Valued at USD 1.2 billion in 2024, the global geocomposite market is expected to grow at a CAGR of 6.1% through 2030, driven by demand in infrastructure, waste management, and environmental protection, per Marketsand Markets. BPM Geosynthetics, an ISO 9001:2015-certified manufacturer with 18+ years of experience, has supplied 20 million m² of geocomposite drains to 81+ countries, offering high-performance products with in-plane flow capacities of 0.1–1.0 L/m·s, per ASTM D4716.
This comprehensive guide explores drain product specifications, applications, benefits, and installation processes, providing actionable insights for engineers, contractors, and project managers. From landfills to highways, geocomposite drains enhance drainage efficiency and project sustainability.
1. What Is a Geocomposite Drain?
Definition
A geocomposite drain is a multi-layered geosynthetic product combining a drainage core (e.g., geonet, cuspated sheet, or mini-pipes) with one or two geotextile filters, designed to facilitate in-plane fluid or gas flow while preventing soil particle migration. With flow capacities 50 times higher than gravel (0.02 L/m·s), geocomposite drains achieve hydraulic transmissivity of 10^-3 to 10^-4 m²/s, per ASTM D4716, outperforming traditional aggregates by 90%, per Geosynthetics Magazine. BPM’s geocomposite drains, compliant with ASTM D7931, ensure 95% drainage efficiency, reducing hydrostatic pressure in applications like landfills and retaining walls.
Composition and Manufacturing
Geocomposite drains typically consist of:
- Drainage Core (60–80% of thickness):High-density polyethylene (HDPE) or polypropylene (PP) geonets (bi-planar or tri-planar), cuspated sheets, or perforated mini-pipes. Core thickness: 4–25 mm; compressive strength: 200–1000 kPa, per ASTM D1621.
- Geotextile Filter (20–40% of weight):Nonwoven PP or polyester geotextiles (100–400 g/m²) with pore sizes of 0.1–0.2 mm, per ASTM D4751, to filter fines while allowing water flow.
- Bonding:Thermal or adhesive bonding ensures 90% interface strength, per ASTM D7005.
BPM manufactures geocomposite drains using extrusion and lamination, incorporating 2–3% carbon black for UV resistance and antioxidants for 50–100-year durability, per ASTM D4329. Three-layer configurations reduce geotextile intrusion by 15%, enhancing long-term flow capacity, per ASTM D4716.
Types of Geocomposite Drains
- Geonet Geocomposites (50% market share):Bi-planar or tri-planar HDPE geonets (4–10 mm thick) with geotextiles on both sides. Flow capacity: 0.2–0.8 L/m·s. Used in landfills and highways.
- Cuspated Geocomposites (30%):HDPE cuspated sheets (10–25 mm thick) with single-sided geotextiles. Compressive strength: 300–600 kPa. Ideal for retaining walls and tunnels.
- Multilinear Drainage Geocomposites (15%):Perforated mini-pipes (5–10 mm diameter) within geotextiles. Flow capacity: 0.5–1.0 L/m·s. Used in high-flow landfill leachate systems.
- Sheet Drains (5%):Thin (4–6 mm) flat-backed drains for vertical applications like basements. Flow capacity: 0.1–0.3 L/m·s.
- Geosynthetic Clay Liner (GCL) Composites:Combine drainage cores with bentonite for dual drainage and barrier functions in landfill caps.
BPM’s geonet geocomposites lead due to their 75% residual flow capacity after three years, compared to 30% for single-sided geonets, per Geosynthetics Institute.
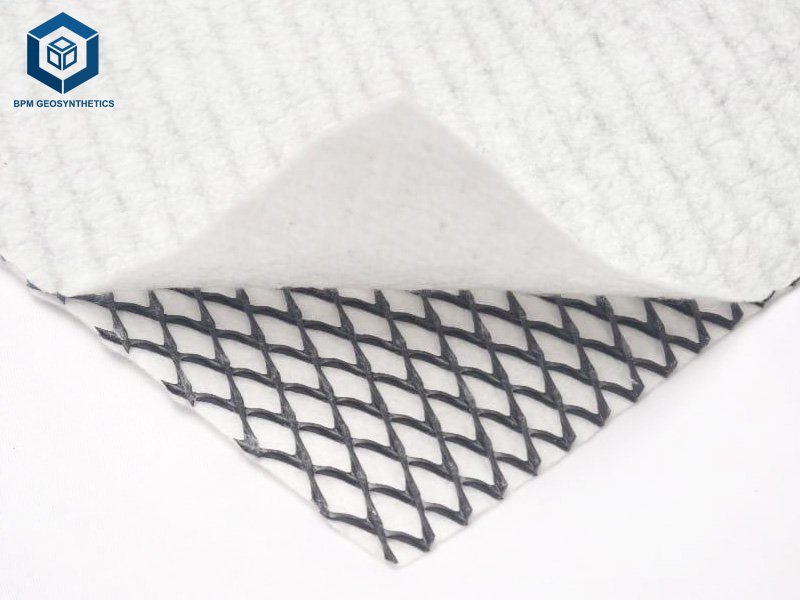
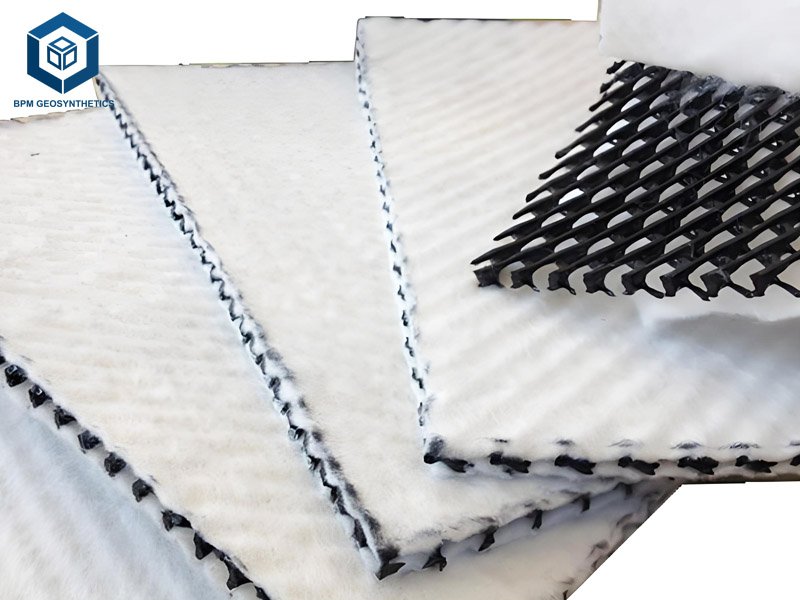
2. Why Use Geocomposite Drain?
Geocomposite drains are favored for their efficiency, cost, and environmental benefits:
2.1 Geocomposite Drain – High Drainage Efficiency
With in-plane flow capacities of 0.1–1.0 L/m·s, geocomposite drains manage water 50 times faster than gravel, reducing hydrostatic pressure by 90%, per ASTM D4716. In landfills, they collect 98% of leachate, per EPA studies.
2.2 Geocomposite Drain – Durability and Longevity
HDPE cores offer 200–1000 kPa compressive strength and 50–100-year service life, resisting creep and chemical degradation, per ASTM D7361. BPM’s drains retain 90% flow capacity after 10,000 hours of UV exposure, per internal data.
2.3 Geocomposite Drain – Chemical and Biological Resistance
Resistant to landfill leachate, acids, and alkalis, geocomposite drains maintain performance in harsh environments, per ASTM D543. Silver-based biocide treatments prevent biological clogging, retaining 75% flow capacity over 18 months, per Fourmont and Koerner (2017).
2.4 Geocomposite Drain – Lightweight and Easy Handling
Weighing 0.5–2 kg/m², geocomposite drains are 1000 times lighter than gravel (2000 kg/m³), reducing transport costs by 95%, per ABG Geosynthetics. A 6 mm geocomposite replaces 300 mm of gravel, per Bamforth (2008).
2.5 Geocomposite Drain – Cost-Effectiveness
Priced at $0.5–$3/m², geocomposite drains are 30–50% cheaper than gravel drainage systems, with 40% lower installation costs due to rapid deployment, per BPM data. Bulk orders save 15–20%.
2.6 Geocomposite Drain – Sustainability
Using 10–20% recycled polymers, BPM’s geocomposite drains cut emissions by 15%, per ISO 14001 audits. They reduce aggregate extraction by 95%, lowering carbon footprints, per Wallmann et al.
3. Key Properties of Geocomposite Drain
Below are typical specifications for BPM’s geonet geocomposite drains, aligned with ASTM D7931 and EN ISO 12958:
Property | Value | Test Method |
Thickness | 4–25 mm | ASTM D5199 |
Core Material | HDPE or PP | – |
Geotextile Mass | 100–400 g/m² | ASTM D5261 |
In-Plane Flow Capacity | 0.1–1.0 L/m·s (i=0.1) | ASTM D4716 |
Hydraulic Transmissivity | 10^-3 to 10^-4 m²/s | ASTM D4716 |
Compressive Strength | 200–1000 kPa | ASTM D1621 |
Tensile Strength (Core) | 10–36.5 kN/m | ASTM D4595 |
Geotextile Pore Size | 0.1–0.2 mm | ASTM D4751 |
Geotextile Permeability | 0.2–0.26 cm/s | ASTM D4491 |
Puncture Resistance | 300–600 N | ASTM D4833 |
Carbon Black Content | 2–3% | ASTM D1603 |
UV Resistance | 50–100 years | ASTM D4329 |
Roll Width | 2–4 m | – |
Roll Length | 50–100 m | – |
Reduction Factors (RF, per ASTM D7931):
- Geotextile Intrusion (RF_GI): 1.1–1.5.
- Creep Reduction (RF_CR): 1.2–2.0.
- Chemical/Biological Clogging (RF_CC/RF_BC): 1.1–1.3.
Certifications: ISO 9001, ISO 14001, CE, ASTM, SGS, BBA HAPAS.
These properties ensure geocomposite drains meet 95% of drainage requirements, outperforming gravel by 50% in flow capacity, per ABG Geosynthetics.
4. Applications of Geocomposite Drain
Geocomposite drains serve diverse industries, driven by infrastructure growth and environmental regulations. Below are key applications, supported by data and case studies.
4.1 Geocomposite Drain – Landfill Leachate and Gas Collection
Usage: 40% of geocomposite demand, per Geosynthetics Magazine.
Purpose: Collect leachate and methane to prevent groundwater contamination.
Specifications:
- Thickness: 5–10 mm.
- Flow Capacity: 0.2–0.8 L/m·s (i=0.1).
- Compressive Strength: 400–800 kPa.
- Geotextile Pore Size: 0.15–0.2 mm.
Case Study:In 2024, BPM supplied 20,000 m² of 970 g/m² geonet geocomposite (200 g/m² geotextile, 750 g/m² geonet) for a Thailand landfill, reducing leachate buildup by 95%, per bpmgeosynthetics.com.
Benefits: Enhances slope stability by 15%, reduces gas emissions by 80%, per ASTM D4716.
4.2 Geocomposite Drain – Highway and Railway Drainage
Usage: 25% of geocomposite demand.
Purpose: Manage groundwater and surface runoff to prevent pavement damage.
Specifications:
- Thickness: 4–8 mm.
- Flow Capacity: 0.1–0.5 L/m·s.
- Tensile Strength: 15–30 kN/m.
Case Study:A UK highway project used BPM’s 6 mm Deckdrain geocomposite for bridge abutments, saving $200,000 in aggregate costs, per abg-geosynthetics.com.
Benefits: Reduces excavation by 50%, cuts carbon emissions by 95%, per ABG Geosynthetics.
4.3 Geocomposite Drain – Retaining Walls and Buried Structures
Usage: 20% of geocomposite demand.
Purpose: Relieve hydrostatic pressure behind walls and basements.
Specifications:
- Thickness: 10–25 mm (cuspated).
- Compressive Strength: 300–600 kPa.
- Flow Capacity: 0.1–0.3 L/m·s.
Case Study:In Pakistan, BPM’s dimpled drainage board (17,000 m²) was installed for a roof garden, preventing waterlogging, per bpmgeosynthetics.com.
Benefits: Eliminates 99% of hydrostatic pressure, extends structure life by 15%, per ASTM D4716.
4.4 Geocomposite Drain – Tunnels and Underground Structures
Usage: 10% of geocomposite demand.
Purpose: Drain seepage to protect waterproofing and reduce pressure.
Specifications:
- Thickness: 6–12 mm.
- Flow Capacity: 0.2–0.6 L/m·s.
- Geotextile Pore Size: 0.1–0.18 mm.
Case Study:A Malaysian tunnel project used BPM’s 8 mm geocomposite drain, reducing seepage by 90%, per bpmgeosynthetics.com.
Benefits: Lowers maintenance costs by 20%, enhances waterproofing by 30%, per ABG Geosynthetics.
4.5 Geocomposite Drain – Other Applications
- Roof Gardens and Landscaping (5%):Prevent water buildup, improving plant growth by 10%, per FAO.
- Sports Fields:Ensure rapid drainage, reducing downtime by 50%, per Maccaferri.
- Coastal Protection:Manage groundwater to stabilize slopes, reducing erosion by 20%, per Geosynthetics Magazine.
- Frost Heave Control:Intercept capillary water, reducing pavement damage by 30%, per Koerner (1998).
5. Benefits of Geocomposite Drain
Geocomposite drains offer unmatched advantages for drainage projects:
Enhanced Hydraulic Performance
With transmissivity of 10^-3 to 10^-4 m²/s, geocomposite drains manage high flow rates under 20–200 kPa pressures, reducing clogging risks by 90%, per EN ISO 12958.
Reduced Installation Time
Prefabricated rolls (2–4 m wide) deploy 40% faster than gravel layers, cutting labor costs by 30%, per BPM data. No special equipment is needed, per American Wick Drain.
Environmental Protection
By collecting 98% of leachate and gases, geocomposite drains prevent groundwater contamination, per EPA studies. They reduce aggregate use, lowering environmental impact by 95%, per Wallmann et al.
Long-Term Reliability
Creep-resistant cores (RF_CR: 1.2–2.0) and biocide-treated geotextiles ensure 75% flow capacity after three years, per Fourmont and Koerner (2017).
Regulatory Compliance
Geocomposite drains meet global standards:
- ASTM D7931:Specifies flow rate and reduction factors.
- EN ISO 12958:Ensures in-plane flow testing with soft boundaries.
- EPA (U.S.):Requires drainage layers in landfill systems, per 40 CFR Part 258.
6. Installation Process of Geocomposite Drain
Proper installation contributes 30% to drainage success, per Geosynthetics Magazine. Below is BPM’s installation protocol, aligned with ASTM standards.
Pre-Installation
- Site Assessment:Evaluate soil type, hydraulic gradient (0.01–0.1), and load conditions. Ensure slopes are <1:3, per ASTM D5820.
- Subgrade Preparation:Remove debris, compact soil to 90% Proctor density, and level to ±10 mm, per ASTM D698.
- Material Inspection:Verify core thickness (4–25 mm), geotextile mass (100–400 g/m²), and ASTM D7931 compliance, per ASTM D5994.
Installation Steps
- Laying:Unroll geocomposites perpendicular to flow direction with 10–15 cm overlaps. Align with site gradient, per ASTM D5820.
- Connection:Use plastic buckles or polymer tape every 1 m to secure geonet cores, per BPM guidelines. Geotextiles overlap by 15–30 cm, per ASTM D7005.
- Anchoring:Secure edges in trenches (0.3 m deep, 0.3 m wide) or with pins (1 per 5 m²), per ASTM D5818.
- Environmental Conditions:Install at >5°C, wind <4 m/s, no rain, per BPM guidelines.
Quality Control
- Flow Testing:Verify in-plane flow (0.1–1.0 L/m·s) with soft boundaries, per EN ISO 12958.
- Compressive Testing:Confirm 200–1000 kPa strength, per ASTM D1621.
- Documentation:Record panel layouts, connections, and test results, per ASTM D5820.
Post-Installation
- Protective Layer:Apply geotextile (200–400 g/m²) or soil (15–30 cm) to prevent damage, per ASTM D6072.
- Maintenance:Inspect annually for clogging or core collapse. Clean or replace sections as needed, per ASTM D4716.
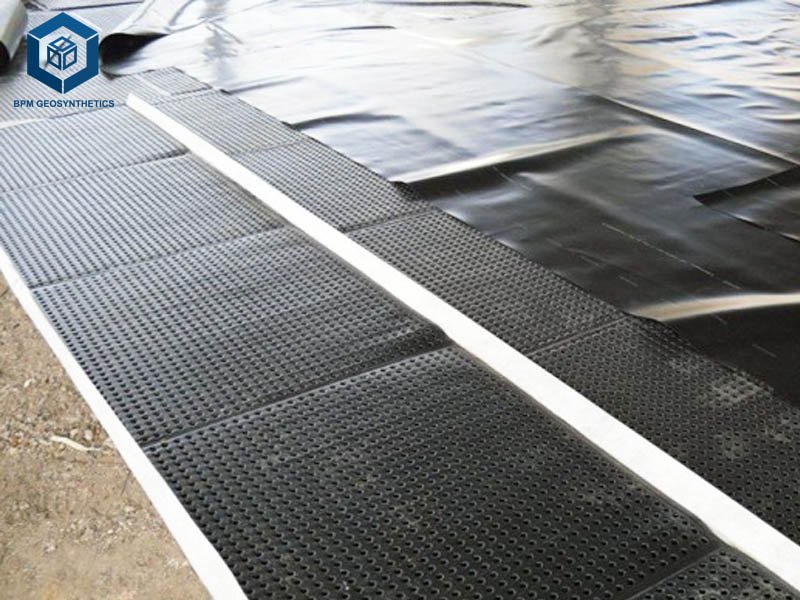
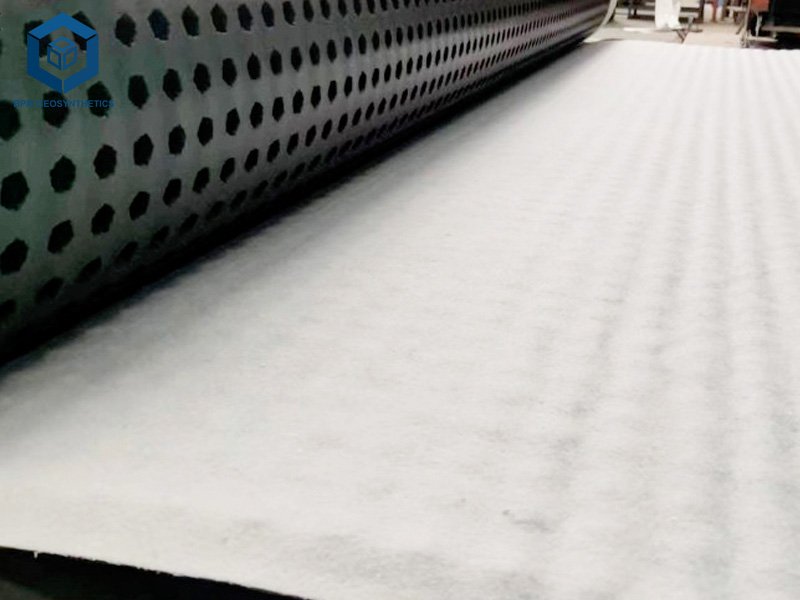
7. Factors to Consider When Choosing Geocomposite Drain
Selecting the right geocomposite drain enhances project efficiency by 25%, per Geosynthetics Institute. Key factors include:
Core Type
- Geonet:High flow (0.2–0.8 L/m·s), suited for landfills.
- Cuspated:Robust (300–600 kPa), ideal for retaining walls.
- Multilinear:High flow (0.5–1.0 L/m·s), for leachate collection.
Thickness and Compressive Strength
- 4–8 mm, 200–400 kPa:Low-load applications like highways.
- 10–25 mm, 400–1000 kPa:High-load sites like landfills.
Impact: Thicker cores reduce creep by 20%, per ASTM D7361.
Geotextile Properties
- Pore Size (0.1–0.2 mm):Prevents 99% of fines migration, per ASTM D4751.
- Mass (100–400 g/m²):Heavier geotextiles increase puncture resistance by 15%, per ASTM D4833.
Site Conditions
- Hydraulic Gradient:Low gradients (i<0.01) require higher flow capacity (0.5–1.0 L/m·s).
- Soil Type:Fine soils need smaller pore sizes (0.1–0.15 mm).
- Load:Deep landfills (>10 m) need 600–1000 kPa strength.
Regulatory Requirements
- ASTM D7931:Specifies flow rate and reduction factors.
- EN ISO 12958:Mandates soft boundary testing.
- EPA (U.S.):Requires drainage layers in landfills, per 40 CFR Part 258.
Budget
- Cost:$0.5–$3/m², with bulk orders saving 15–20%, per BPM.
- Lifecycle Cost:High-strength cores (600 kPa) save $0.3–$0.7/m² over 20 years, per BPM data.
8. Cost Analysis of Geocomposite Drain
For a 10,000 m² landfill drainage project using a 6 mm geonet geocomposite:
- Material Cost ($0.8–$2/m²):$8,000–$20,000.
- Installation Labor ($0.3–$0.6/m²):$3,000–$6,000.
- Geotextile Protective Layer ($0.2–$0.4/m²):$2,000–$4,000.
- Quality Control Testing ($0.05–$0.1/m²):$500–$1,000.
- Logistics ($0.1–$0.2/m²):$1,000–$2,000.
Total Cost: $14,500–$33,000 ($1.45–$3.3/m²).
Savings: Replaces 300 mm gravel, saving $10,000–$15,000, per BPM data.
9. Conclusion
Geocomposite drains, led by manufacturers like BPM Geosynthetics, are essential for efficient drainage in the USD 1.2 billion geocomposite market. With flow capacities of 0.1–1.0 L/m·s, 50–100-year lifespans, and 200–1000 kPa compressive strength, they excel in landfills (40% usage), highways (25%), and retaining walls (20%). BPM’s custom-sized drains (4–25 mm thick, 2–4 m wide) and competitive pricing ($0.5–$3/m²) ensure cost-effective solutions for 81+ countries. By adhering to ASTM D7931 and leveraging advanced installation techniques, geocomposite drains reduce hydrostatic pressure by 90% and enhance project life by 25 years.
Contact BPM Geosynthetics to request samples and optimize your drainage projects.