Landfill liner is essential for mitigating the environmental impacts of waste disposal. It play a vital role in protecting water resources and preventing the contamination of surrounding ecosystems. BPM Geosynthetics is the trusted Landfill liner manufacturer and supplier, we offers a wide range of landfill liner material with custom size and thickness at best factory price.
1.1 What Is A Landfill liner?
A landfill liner is a crucial component of landfill design and construction. Its primary function is to prevent the contamination of groundwater and nearby surface water by hazardous substances present in the waste deposited in the landfill. By acting as a low permeable barrier, the landfill liner inhibits the migration of leachate, which is the liquid formed as water percolates through the waste, and its toxic constituents into underlying aquifers or neighboring rivers. This prevents the potential irreversible contamination of local waterways and their sediments.
A typical landfill liner system is composed of various components, which may include:
1.1 Bottom Liner
This serves as the primary barrier between the waste and the underlying soil and groundwater. It is typically made of impermeable materials such as geomembranes (synthetic liners) or compacted clay.
1.2 Leachate Collection System
Situated beneath the liner, this system consists of a network of pipes and collection channels designed to capture leachate. Leachate can contain hazardous substances, so it is crucial to manage and treat it properly to prevent environmental harm.
1.3 Drainage Layer
Some landfill liners incorporate a layer of gravel or sand above the liner. This layer enhances drainage and facilitates the movement of leachate towards the collection system.
1.4 Protective Cover
On top of the waste and liner system, a layer of soil or other materials may be added to provide additional protection, manage odors, and control erosion.
Modern landfills generally require a layer of compacted clay with a specified thickness and a maximum allowable hydraulic conductivity. This clay layer is overlaid by a high-density polyethylene geomembrane. These materials, along with the other components of the liner system, work together to safeguard soil and groundwater resources and prevent the spread of pollution.
2. What Is The Composition of The Landfill liner
2.1 Geomembrane liner
A geomembrane liner is a synthetic membrane used as an impermeable barrier in geotechnical and environmental projects. It is typically made from materials like high-density polyethylene (HDPE), polyvinyl chloride (PVC), or ethylene propylene diene monomer (EPDM). Geomembrane liners offer several important functions in various industries:
- Containment: Geomembranes are utilized to contain liquids, gases, or solids within a specific area. They form a reliable barrier that prevents the migration of contaminants, pollutants, or hazardous materials into the surrounding environment.
- Fluid Control: These liners control the flow and seepage of liquids, including water, chemicals, or industrial fluids. They are used in applications such as reservoirs, ponds, landfills, and wastewater treatment facilities to ensure proper containment and prevent leakage.
- Environmental Protection: Geomembrane liners play a crucial role in protecting the environment by preventing pollution and contamination. They are utilized in projects involving waste management, hazardous material storage, and remediation of contaminated sites.
2.2 Protection Layer
Geotextile is a permeable synthetic textile material commonly used in geotechnical and civil engineering applications. It is manufactured from synthetic fibers like polypropylene or polyester and is designed to provide various functions:
- Filtration: Geotextiles act as filters by allowing water to pass through while retaining soil particles. They are used in drainage systems, retaining walls, and erosion control applications to prevent the clogging of soil or aggregate layers.
- Separation: Geotextiles separate different materials, such as soil and granular materials, to prevent mixing and ensure proper performance of the engineered structure. They are commonly used in road construction, railways, and landfills to create a separation layer between the subsoil and the base materials.
- Reinforcement: Geotextiles improve the mechanical stability and strength of soil by distributing loads, reducing soil settlement, and enhancing load-bearing capacity. They are utilized in applications such as embankments, slopes, and retaining walls to reinforce the soil structure.
- Erosion Control: Geotextiles help control soil erosion by stabilizing slopes and preventing the loss of soil particles due to water flow. They are used in erosion control blankets, sediment control barriers, and shoreline protection projects.

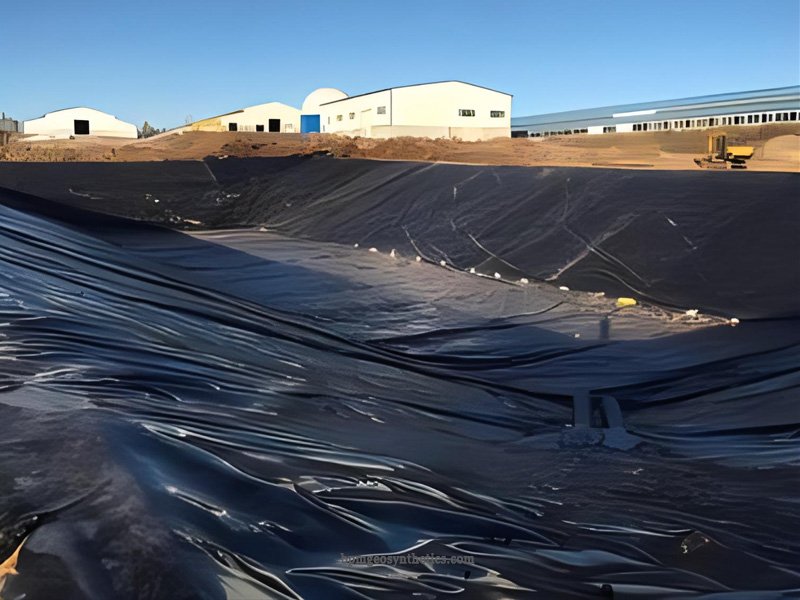
3. What Is The Function of Landfill Liner?
3.1 Prevent Waste Leakage
The primary function of a landfill liner, particularly the geomembrane, is to serve as an impermeable barrier that prevents waste from leaking into the soil and groundwater. It acts as a reliable containment system that ensures the waste remains within the designated landfill area.
3.2 Prevent Environmental Pollution
By effectively containing the waste within the landfill, the presence of the landfill liner helps reduce or eliminate the risk of pollution to the soil, groundwater, and the surrounding environment. It prevents the migration of hazardous substances and leachate, which could potentially contaminate nearby ecosystems and water sources.
3.3 Improve Landfill Stability
The landfill liner plays a role in enhancing the stability of the landfill structure. It helps minimize the risk of foundation settlement and soil erosion by acting as a barrier between the waste and the underlying soil. This contributes to the overall integrity of the landfill, reducing the likelihood of soil instability and potential damage to surrounding areas.
The landfill liner is a critical component in landfill design and operation. It ensures the containment and proper management of waste, preventing environmental pollution and safeguarding soil and groundwater resources. Additionally, the landfill liner contributes to the overall stability and longevity of the landfill structure, providing a secure and sustainable waste disposal solution.
4. How To Design A Landfill Liner System?
High-density geomembranes are extensively utilized in landfill liner design due to their exceptional impermeability and ability to safeguard soil and groundwater resources from seepage. These geomembranes, characterized by their strength, ease of construction, and sustainability, serve as vital protective barrier materials in landfill projects.
The design of a geomembrane for landfill liners involves several considerations to ensure its effectiveness and long-term performance. These considerations may include:
Material Selection: High-density geomembranes, such as those made from HDPE, PVC, or EPDM, are chosen based on their durability, resistance to chemical degradation, and impermeability. The specific material selection depends on factors like site conditions, waste composition, and anticipated lifespan of the landfill.
Thickness: The thickness of the geomembrane is determined based on factors such as the expected waste load, hydraulic conductivity requirements, and design life of the landfill. Thicker geomembranes provide increased resistance to puncture, tear, and degradation.
Anchoring and Seaming: Proper anchoring and seaming techniques are crucial to ensure the integrity of the geomembrane liner. Anchoring methods, such as ballasting or embedment, prevent the liner from shifting or uplifting. Seaming techniques, like thermal welding or extrusion, are employed to create strong and leak-proof joints between geomembrane panels.
Slope Stability: In landfill designs with slopes, additional considerations are made to ensure slope stability and prevent geomembrane damage. Measures such as slope geometry, geosynthetic reinforcement, and erosion control techniques are implemented to maintain the stability of the liner system.
Compatibility with Other Components: The geomembrane design should consider compatibility with other components of the landfill liner system, such as geotextiles, drainage layers, and protective covers. Proper integration and compatibility ensure optimal performance and longevity of the entire liner system.
The design of a geomembrane for landfill liners aims to provide reliable impermeability, protect soil and groundwater resources, and ensure long-term performance. By considering factors like material selection, thickness, anchoring, seaming, slope stability, and compatibility, engineers can create effective and sustainable landfill liner designs that minimize the potential for environmental contamination.
5. How To Install Landfill Liner?
HDPE geomembrane construction and installation specifications are as follows:
5.1. Preparation work before laying
- Develop a construction plan according to the construction organization design;
- Select HDPE geomembrane materials according to design requirements;
- Foundation treatment: Remove all sharp and hard objects on the ground that may damage the geomembrane, fill in potholes, level the soil surface or repair the slope surface.
- Laying environment: The outdoor temperature is above 5℃, the wind force is below level 4, and there is no rain or snow.
5.2 HDPE geomembrane laying method
Large bundles of HDPE geomembrane should be laid using tractors, winches and other machinery. If the conditions are not met and small bundles of HDPE films are available, manual laying can also be used. For slope laying, a winch is used to slowly spread it from the top of the slope to the bottom of the slope, and the top and bottom of the slope are buried in fixed ditches.
Lay HDPE membrane in zones and blocks according to the specified order and direction.
When laying HDPE geomembrane, it should be appropriately relaxed and avoid manual bending and damage.
When laying HDPE geomembrane, the joints formed between modules should be T-shaped and not cross-shaped.
There should be no dirt, sand, water (including dew) and other debris that affects the welding quality on the overlapping surface of the HDPE geomembrane weld.
When laying HDPE geomembrane on a slope, its joint arrangement direction should be parallel or perpendicular to the maximum slope line, and it should be laid in a bottom-up order.
At the bends of the slope, the membrane and joints should be properly attached to the slope.
After the HDPE geomembrane is laid, before it is covered with a protective layer, a 20-40Kg sandbag should be placed at the corners of the membrane every 2-5m.
HDPE geomembrane should be naturally relaxed and firmly attached to the supporting surface, and should not be pleated or suspended.
5.3 On-site connection of HDPE geomembrane
Ensuring the integrity of the joints is the prerequisite for ensuring effective isolation and long-term work of the HDPE geomembrane.
The connection work of HDPE geomembrane should not be carried out under adverse weather conditions to ensure the quality of the connection.
In the case of heat sealing, overheating should be avoided to prevent blistering at the joint.
Adhesion between geomembranes made of different raw materials should be avoided as much as possible, and special research should be conducted when unavoidable.
HDPE geomembrane welding method: hot wedge welding method, its advantages:
- There is no need to roughen the surface of the membrane.
- During the welding process, there is no need to add new substances to form the weld.
- Its heat source control is separated from the HDPE geomembrane. The welding form should be double weld overlap, with a line width of 12mm and a clear distance of 10mm between the two lines.
Use clean gauze to wipe the overlap of the weld to ensure that it is free of water, dust and dirt. The geomembrane should be aligned in parallel and overlap appropriately.
Welding quality control: Adjust the welding equipment to the best working condition according to the local climate conditions and material properties at that time. During the welding process, attention should be paid to the selection of temperature, speed and pressure.
Carry out a small sample welding test first, and try to weld a 1m-long HDPE geomembrane sample. Use an on-site tearing inspection test. If the weld is not damaged by tearing and the base material is torn, it is considered qualified.
After passing the on-site tear test, formal welding will be carried out one by one.


6 Precautions for Landfill Liner Welding Seams
6.1 The HDPE geomembrane at the welding seam should be welded into one body, and the welding seam should be free of welding, missing welding, scorching, damage and holes.
6.2 The weld seam must be cut when there is a weak or missing weld on site. Use a welding machine to repair the cut damaged area with a base metal that is more than twice the diameter of the damage.
6.3 The width of the double seam of the weld should be 2mm×10mm
6.4 The offset size between transverse welds should be greater than or equal to 500mm
6.5 T-shaped joints should be patched using the base material, and the patch size can be 300mm×300mm
6.6 The two connected layers of HDPE geomembrane must be overlapped, flat and smooth. ,
7. Landfill Liners weld quality inspection
The detection method should adopt the inflation method, that is, the double weld pressure detection method and the vacuum tank method. The spark test or ultrasonic detection method can also be used.
The testing equipment adopts pneumatic detectors and vacuum detectors.
Weld quality requirements:
- The distance between each section of the double-slit test is about 1.5mm-3mm. The pressure is controlled at 0.5MPa-2.0MPa according to the requirements of the geosynthetic material testing regulations. The time is 30 seconds. If the observation is more than 30 seconds, the gas will not Will leak, then the connection is deemed to be qualified.
- For single welds, T-shaped joints and repair points, a 50cm × 50cm square should be used for vacuum testing. The vacuum pressure should be greater than or equal to 0.005MPa and maintained for 30 seconds. If the soap solution does not foam, it is qualified.
- In indoor testing, the strength of the membrane-to-membrane welding seam shall not be less than 80% of the strength of the base metal (welding shear strength ≥ 80% of the tensile strength of the base metal)
Quality inspection should be carried out at the same time as the construction progresses. The connection quality must be carefully checked. Those that fail must be reworked resolutely.
8. Summary
The lanfill liner of landfill plays an important role in environmental protection and waste management. Further research and innovation will help improve the performance and sustainability of barrier layers.
Any questions or inquiries, please contact us.