HDPE membrane liner, also known as HDPE geomembrane liner, is the kind of cost effective and ideal geosynthetic material for both lining and covering for primary and secondary solid-waste landfills to prevent groundwater contamination beneath, odors, and other environmental applications. HDPE geomembrane liner is available in a variety of surface finishes including smooth, textured and composite. South Africa has always been a mining powerhouse. Diamond and gold production were well down from their peaks since 2013, South Africa is still number five in gold and remains a cornucopia of mineral riches. It is the world’s largest producer of chrome, manganese, platinum, vanadium and vermiculite. It is the second largest producer of ilmenite, palladium, rutile and zirconium. It is also the world’s third largest coal exporter. South Africa is also a huge producer of iron ore. HDPE membrane liner is widely used in those of mining projects.
The Best Project Material Co., Ltd (BPM) is the leading geomembrane manufacturer, supplier, wholesaler and exporter, BPM geomembrane products are widely used across a variety of industries including waste, water, aquaculture, mining, power plant, industrial and civil engineering, etc. BPM brand geomembrane products are made of finest quality high-density polyethylene (HDPE) with specially formulated, virgin polyethylene resin by the state of the art automatic production lines and advanced pressing technology.
Geosynthetic products have become an integral part of the construction process for several key industries. Its price and physical properties are major advantages compared to traditional alternatives. Geosynthetics are manufactured from various man made polymers and are used in conjunction with soil or rock to enhance the stability of terrains. These products are used in civil, mining and transport infrastructure projects because of its ability to solve a range of engineering problems related to soil reinforcement, erosion control and containment. Geosynthetic products are classified into four types. Geomembranes, geotextiles, geocells and geocomposites. The most popular of these types is geomembrane.
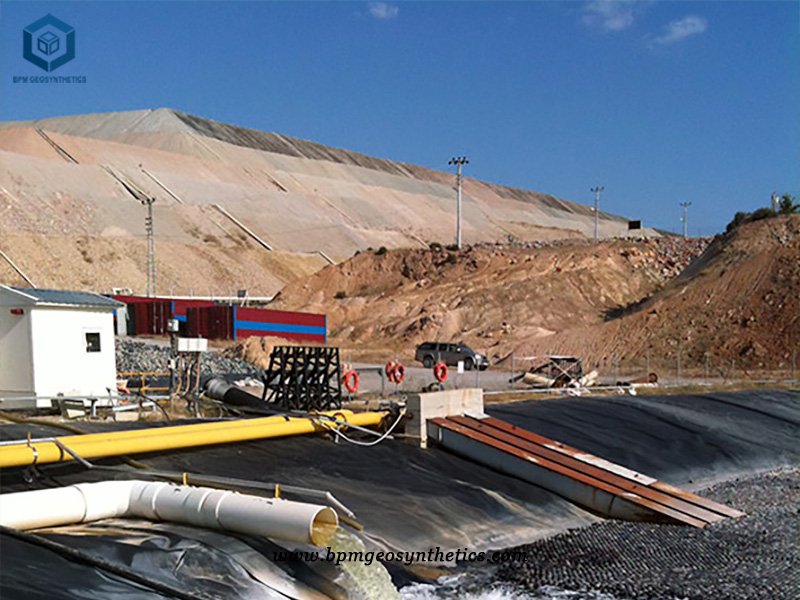
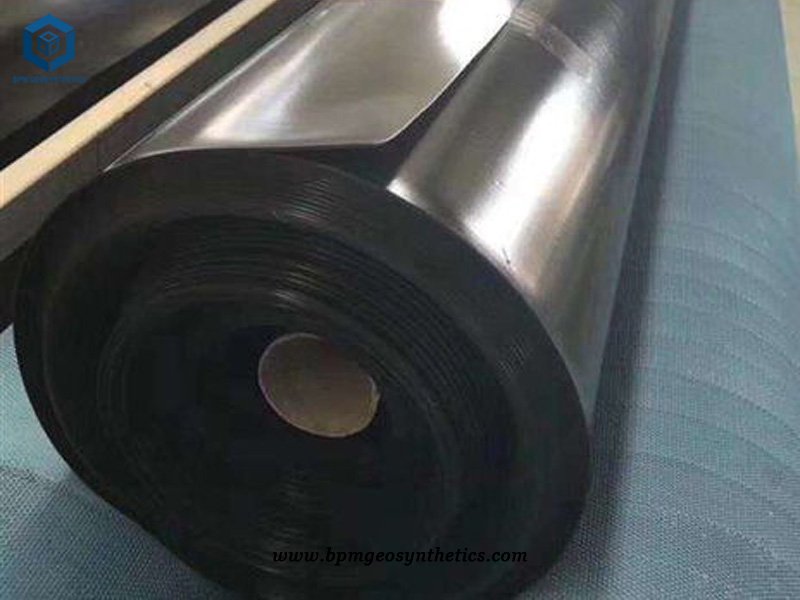
Geomembranes are made from impermeable geosynthetic material consisting of thin continuous sheets of polymers. HDPE membrane liner can create an impermeable barrier that prevents the leakage of harmful contaminants or dangerous chemicals to surrounding environments. It is also regularly used as containment barriers for potable water and irrigation storage requirements to prevent leakage. Geomembrane liner is used in conjunction with other geosynthetic products to control fluid movement and provide containment in projects related to mining, sewage treatment and canal construction.
The application of geomembrane in the mining industry started in the 1970s and has increased thereafter. It is used as a lining solution for evaporation ponds, heap leach pads and tailing impoundments. The design and construction of these heap leach pads are regulated to protect the environment from exposure to harmful chemicals so a lining system, usually a HDPE geomembrane, forms a critical component in construction of these heap leach facilities.
HDPE geomembrane liner is also used during the end of a mine’s lifespan. As a part of mine restoration, HDPE membrane liner liner is used to seal the mine and prevent waste products from contaminating the surrounding environment. Overall, geomembrane lining is a safe and effective solution to protect the environment from harmful industries.
Installing geomembrane lining systems is a complicated process that is generally carried out by trained engineers and technicians. Various specialized welding techniques, site preparation, and installation expertise are required to ensure that any geomembrane lining system is properly employed. The following is a general, yet illustrative, geomembrane installation process:
Quality Assurance Inspection: The following items are reviewed to ensure quality geomembrane installation:
- Surface conditions met all requirements before the HDPE membrane liner was laid.
- The geomembrane liner rolls were deployed and identified correctly.
- The anchor system was done correctly.
- The anchor trench and the placement of the lining were all done correctly.
- The correct welding equipment was used.
- The quality control devices were operating correctly.
- Verified the fusion welding seaming and/or extrusion welding seaming.
- All repairs were completed.
- Correct pipe penetration.
- The seam crossings were accurate.
- The installation was done per the original design.
- The documentation of the installation was completed.
Quality assurance is an ever present standard. Before, during and once the project is complete. Supervisors maintain a presence on the work site at all times to ensure that all the geomembrane installation procedures are correctly implemented. Detailed logs are maintained to record work progress, as well as any issues that occur and how they were resolved. In turn, these records are reviewed by a field manager, providing one further layer of quality assurance inspection.
Pre- Field Installation: Preparing for the installation is the initial step. The following decisions need to be considered:
- Specifications of the geomembrane that will be used.
- The type of anchoring system that is needed.
- The quantity of geomembrane lining.
- Which quality controls will be in place.
- What are the weather conditions as temperatures play a significant role in if and how the installation process will be completed.
Receiving, Storing and Handling: The following factors need to be considered when the product arrives.
- It is required that each roll have an identification number and quality certificate.
- Unload the rolls with approved equipment to prevent damage. Spreader bars or lifting straps can be utilized to accomplish this.
- Visual inspection of the outside of the rolls should reflect that there are no holes, tears or bubbles. Any non-conformance damage that is identified will be noted and recorded. Non-conforming material will either be repaired to conformity, or used in a manner that is appropriate to its use.
- The surface of the storage area needs to be free of stones and any items that could puncture the linings, mud, grease and chemicals. The rolls can be placed on wood platforms or sandy mattresses. The surface should also not be near a heat source. Rolls should not higher than 3 on top of one another
- The storage location needs to be in a location that minimizes the handling of the lining.The actual geomembrane installation has many steps within the entire process.
While the installation process is an involved endeavor, the required effort only illuminates the utility of geomembrane lining systems as a proven commodity for pollution containment.
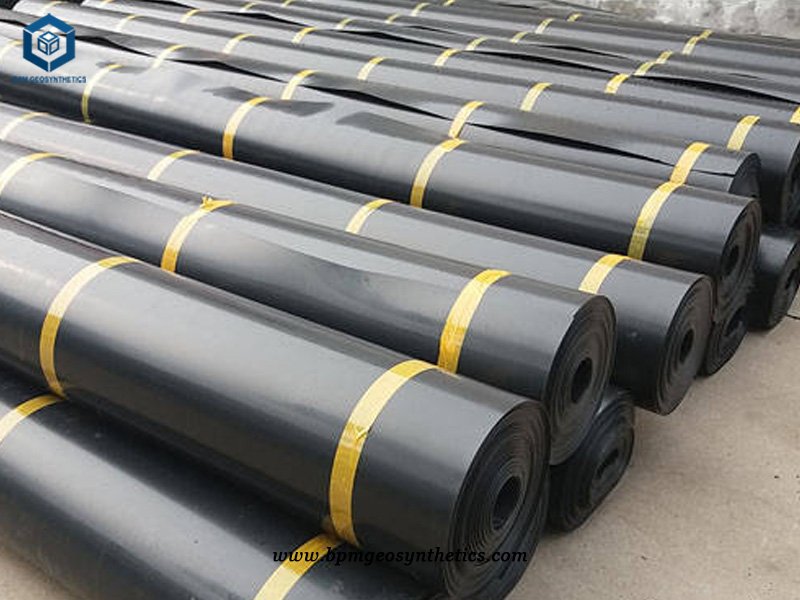
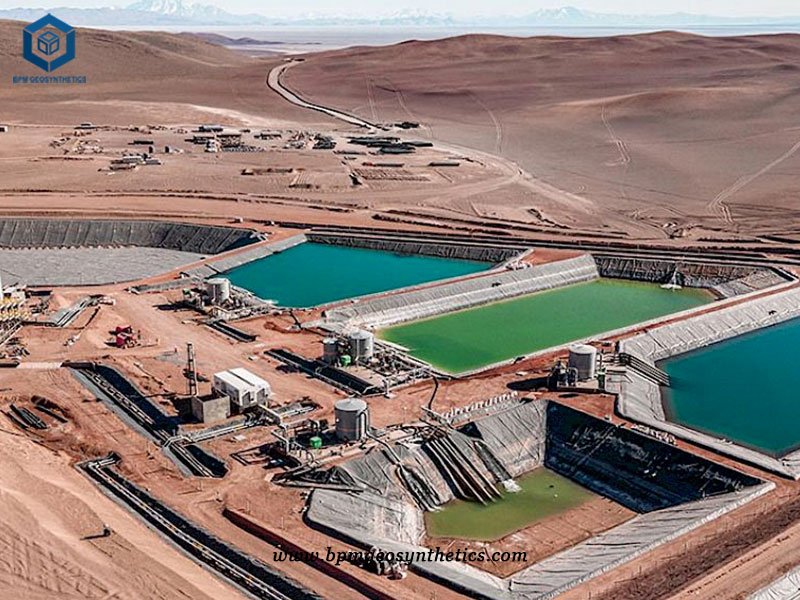
Relevant Regulations
Quality standards are crucial when purchasing geomembrane liner for your project. HDPE geomembrane’s physical properties such as tensile strength and tear resistance are calculated based on test methods specified by ASTM and GSI.
ASTM International
Because of their extensive history in this field, the American Society of Testing and Materials (ASTM) is responsible for the bulk of generic geomembrane test methods.
Geosynthetic Institute (GSI)
Geosynthetic Institute (GSI) is a group of organisations involved in geosynthetics. They provide comprehensive standards, specifications, guidelines and practices for all types of polymeric geosynthetic materials through Geosynthetic Research Institute (GRI.)
Manufacturing Process of HDPE Membrane Liner
The process begins by choosing the suitable polymer resin which is normally in pellet form. Next, different additives such as carbon black, plasticizers, antioxidants and lubricants are added. The formulation of resin and additives are then fed into a hopper which leads to an horizontal extruder. This formulation is transported via a continuous screw through feed section, compression, metering and filtering stages, after which it is pressure fed into a die to create sheets of varying widths and thicknesses by calendering.
Additives are added in the formulation to prevent oxidation and increase durability. Carbon black is sometimes added to the formulation to improve its stability under ultraviolet light, making black HDPE one of the most UV resistant products on the market.
Geomembrane Durability. Several factors affect the degradation of polymers within the geomembranes. Factors like UV exposure, chemical impact, biological contaminants (animal, fungi) and thermal expansion impact the life span of the geomembranes. Technical expertise is necessary when selecting the right type and thickness for the project. This is generally based on the depth of the containment and the geo technical conditions of the site. Please see the corresponding depth and thickness chart for a general overview. This is for guidance only, speak to one of our technical consultants for advice relevant to your requirements.
Conclusion
Determining the best type of HDPE membrane liner for your project can be challenging. Several factors such as cost, availability and applicability come into play. Of all the geomembrane types, HDPE membrane liner is the most recommended because of its operational advantages. It complies with the environmental sustainability requirements, is cheaper than other geomembrane types and has a variety of applications. With its excellent mechanical qualities and long durability, HDPE geomembrane is a cost-effective solution for seepage control and leakage prevention in reservoirs and dams.
Specifications of HDPE Membrane Liner for Tailings Dam Project in South Africa
- HDPE Membrane Liner thickness – 1.5mm
- Total Quantity- 35,280 Square meters
- Each roll Size- 7m*150m
- Standard- ASTM GM13 standard
About BPM
BPM has been specializing in delivering one stop geosynthetics products and solutions to worldwide customers since its foundation in 2007. BPM had provided many types of effective and state of the art geomembranes, geotextiles, geocells, geosynthetic clay liners (GCLs), drainage boards, geogrids to over 81 countries. Our main customers are from Australia, France, Sweden, UK, Hong Kong, Hungary, New Zealand, Poland, Mexico, Ecuador, Brazil, Pakistan, Bangladesh, Thailand, Vietnam, Malaysia, Indonesia, Singapore, Philippines, Sri Lanka, India, UAE, Saudi Arabia, Qatar, Kenya, Ghana, Ethiopia, Somalia, Nigeria, South Africa, Swaziland, Mongolia, etc.
BPM is not only manufacturing best quality geosynthetic products but also providing professional design and installation service. OEM, ODM, custom development and fabrication are also available. If you have any questions or inquiries, please fill and submit the following form, we will reply as soon as possible.