HDPE geosynthetic membrane, also known as HDPE geomembrane liner, is the kind of anti-seepage geotechnical material which is widely used for waste containment, water containment, aquaculture, industrial project, energy project and mining project, etc. HDPE geomembrane liner has the characteristics of anti-seepage property, excellent chemical resistance, outstanding stress cracking ability, low permeability, good UV resistance and low temperature resistance to brittleness, etc. So the HDPE geosynthetic membrane liner is the most widely used for many kinds of anti-seepage bottom pond lining and covering applications such as landfill project, biogas digester projects, sludge and sewage treatment facilities, evaporation ponds for animal manure facilities such as dairy farms and pig farms and chicken Farms.
BPM Malaysian customer contacted us to purchase HDPE geomembrane, and we sent him geomembrane landfill liner samples and product information in time. In August 2019, we mailed geosynthetic membrane samples to customers, we provided samples to TRI Suzhou Office for testing in October, 2019, and the customers and others participated in the whole process of testing. Due to the strict requirements of the project and the understanding of our factory and the company, they visited our HDPE geomembrane manufacturing factory, and finally confirmed the quality of HDPE membrane liner of our company, and signed an order contract with us. They stayed in the factory for 2 days to supervise the production until the container is loading. BPM customer was very satisfied with our geosynthetic membrane and hope to cooperate more with BPM in the future.
Specifications of HDPE Geosynthetic Membrane Liner for Landfill Project in Malaysia
- HDPE Membrane Linerthickness – 1.5 mm
- Total Quantity- 120,000 Square meters
- Each roll Size- 7m*140m
- Standard- ASTM GM13 standard

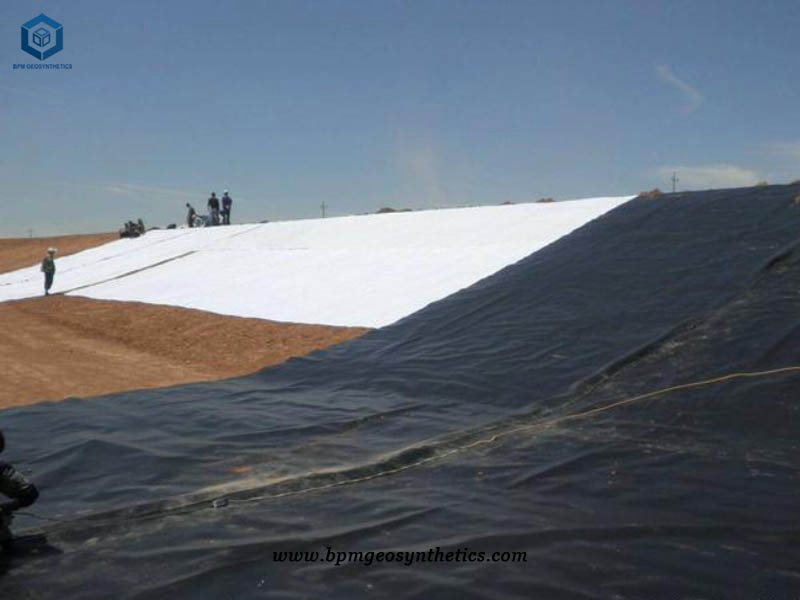
Effect of HDPE Membrane Liner on landfill site
It is the most important part of landfill to prevent the environmental pollution of landfill gas and leachate. The careful consideration of landfill gas and leachate needs to run through the whole life cycle of landfill from design, construction, operation to closure and post closure management. The anti-seepage system at the bottom of reservoir is an important facility to prevent landfill gas and leachate pollution and prevent groundwater and surface water from entering the landfill.
The horizontal seepage control system of landfill site usually includes filter layer, drainage layer, protective layer and impervious layer from top to bottom. The impervious layer is the most important layer in the horizontal anti-seepage system. Its function is to lay low-permeability materials in the landfill site to prevent the leachate from migrating to the environment outside the landfill site; the impermeable layer can also block the surface water and groundwater from entering the landfill site. The liner system of horizontal seepage control can be divided into single liner system, composite liner system, double liner system and multi liner system.
The impervious layer is made of impervious material with less water permeability. There are three kinds of materials suitable for landfill seepage control system: inorganic natural anti-seepage materials, natural and organic composite anti-seepage materials and artificial synthetic organic materials. HDPE geosynthetic membrane liner is widely used for landfills.
HDPE geosynthetic membrane liner is the most commonly used anti-seepage material in synthetic materials. At present, most of the landfills in the United States have adopted two-layer HDPE geomembrane for seepage control, and the design standards for toxic and hazardous waste landfills are even higher. In the early 1990s, China began to use HDPE geomembrane as the main anti-seepage material for landfill site. HDPE geosyntheitc membrane is not only used as the main material of anti-seepage system of landfill bottom and side wall, but also widely used as the main anti-seepage layer of landfill cover system and anti-seepage liner of leachate regulating pool. Therefore, the application of HDPE geosynthtice membrane seepage control technology in domestic landfill has a very broad development prospect.
The main characteristics of HDPE membrane are stable chemical properties, landfill leachate will not pose a threat to it; low permeability, to ensure that groundwater and rainwater infiltration liquid will not seep through the liner, methane gas will not overflow the drainage system; stable UV resistance, carbon black in HDPE enhances the anti ultraviolet ability.
- The permeability coefficient K is less than 10-12cm/s;
- It has good chemical stability and corrosion resistance to most chemical substances;
- The mechanical strength is high;
- For the convenience of construction, a series of matching welding methods have been developed, which are relatively mature in technology;
- High performance;
- It can work well in low temperature.
BPM HDPE geosynthetic membrane liner has the highest quality and the longest service life because it does not use recycled materials. The HDPE geomembrane liner produced by BPM company has the best impermeability, excellent chemical corrosion resistance, outstanding environmental stress cracking resistance, excellent puncture resistance, excellent UV resistance, stable low temperature anti embrittlement performance, with high cost performance.
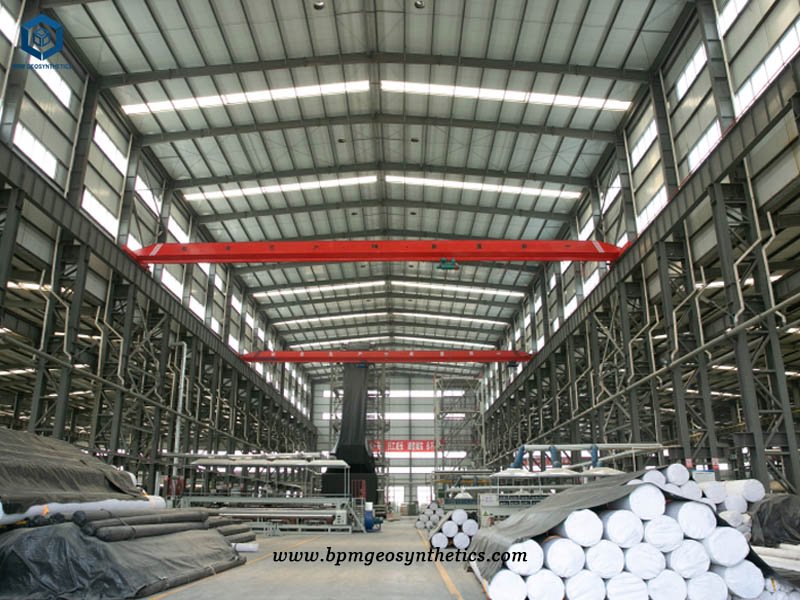
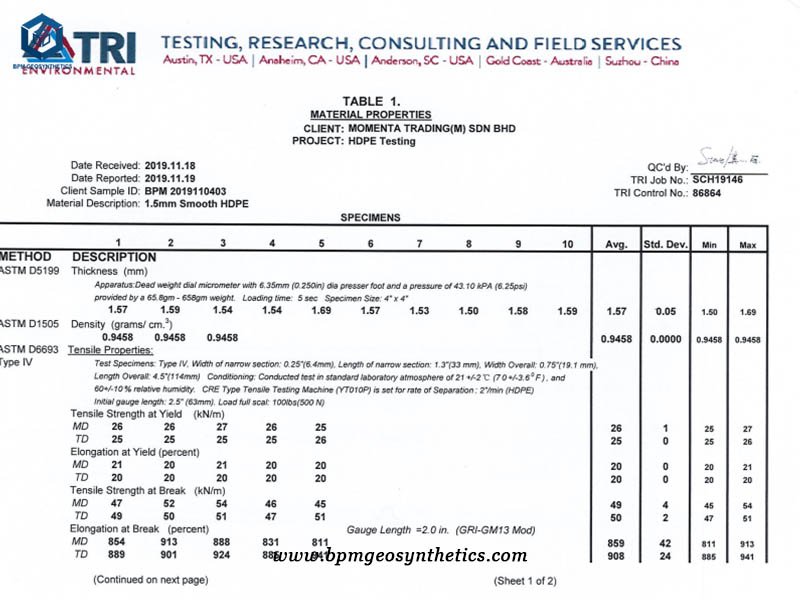
Classification of landfills
1. Solid Waste Landfill. Solid waste landfill especially the Municipal Solid Waste landfills (MSW) now usually requiresa single and/or double composite liner comprised of both a leachate collection and removal system, as well as a geomembrane (overlying either a GCL or compacted clay soil). Being more stringent environmental regulations around the world, HDPE geomembrane liner has been extensively used to line landfills as they offer long term durability as well as excellent chemical resistance to a wide variety of harsh materials. Landfill applications using geosynthetic membrane liner include their use as bottom liners for waste and leachate containment, vertical cutoff walls and landfill closures. Here are several factors to consider when deciding which type of geosynthetic membrane liner to use in a solid waste landfill projects.
- Steep slope angles (Interface friction)
- Low permeability
- High tear and puncture resistance (depending on the type of terrain)
- Chemical resistance
- Temperature range
- Duration of the project
- V exposure
- Hydrostatic pressure
- Tensile and elongation properties
2.Hazardous waste landfill. Modern hazardous waste landfills are highly engineered endeavorsand are part of an overall integrated hazardous waste management system. Disposal in a hazardous waste landfill represents the last step in the treatment or waste handling process, thereby providing long term confinement or control of hazardous materials.
Specifically designed to prevent contamination of the environment, hazardous waste landfills generally require double-liner systems (two geomembranes), often incorporating both GCLs and compacted clay soil. HDPE geosynthtic membrane liner is extensively used in double-lined systems providing a greater level of safety and protection for the surrounding environment and offering a more effective method of capturing and collecting leachate. Here are several factors to consider when deciding which type of geomembrane to use in hazardous waste landfill.
- Steep slope angles (Interface friction)
- Low permeability
- High tear and puncture resistance (depending on the type of terrain)
- Chemical resistance
- Temperature range
- Duration of the project
- V exposure
- Hydrostatic pressure
Tensile and elongation properties
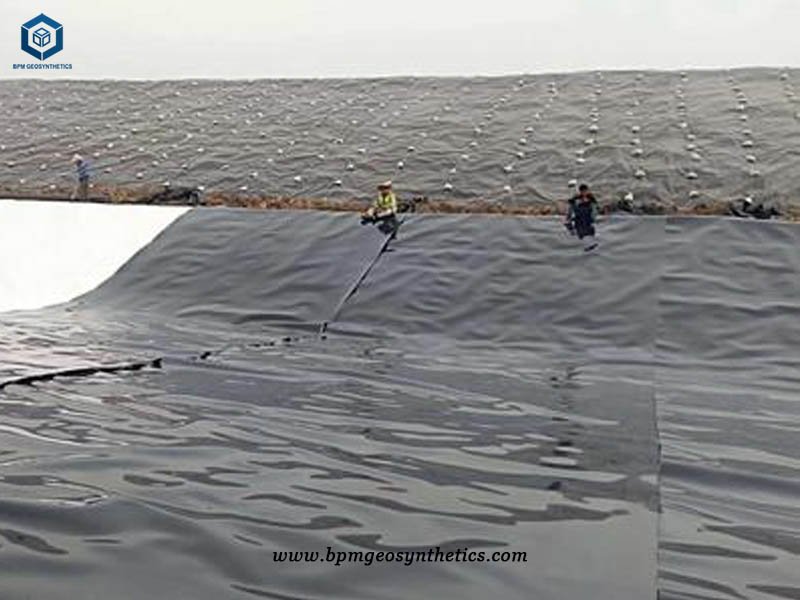
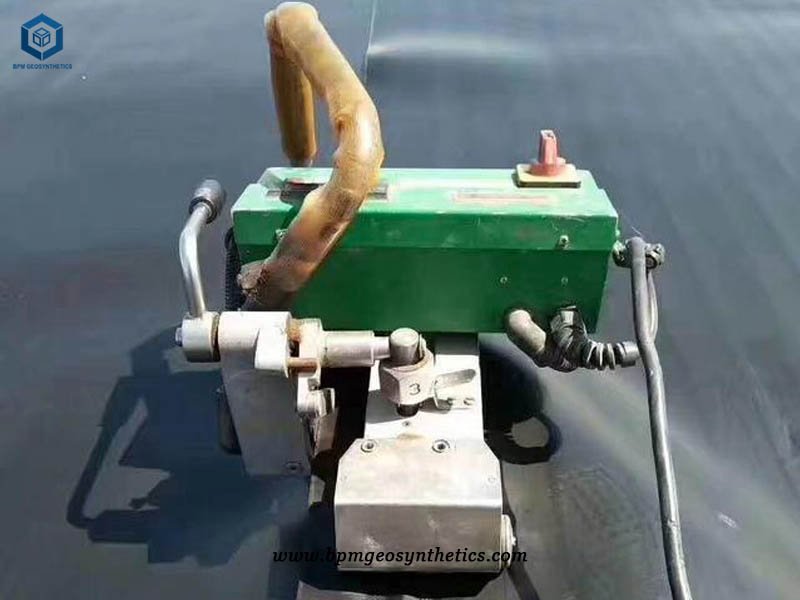
Construction process of HDPE Geosynthetic Membrane for Landfill Project
1. Construction preparation for landfill site (construction of impervious HDPE geomembrane liner). After leveling the bottom of the landfill site, according to the design requirements, the underground water collection pipe trench is manually excavated, the remaining soil is transported to the surrounding area of the reservoir bottom, the anti-seepage material is laid from bottom to top, the gravel groundwater diversion layer membrane material and the upper and lower layer geotextile are laid. After the inspection, the prepared pebble stones are paved with machinery and manual. The concrete operation is as follows: the plastic film and the upper layer geotextile of the reservoir dam shall be laid first. After the plastic film and the upper layer geotextile are laid and accepted, one excavator shall be arranged at the bottom and top of the dam respectively to transport the pebble diversion layer to the reservoir dam slope, and then level it manually. In order to ensure the laying quality, membrane material laying and diversion layer should be carried out equally and constructed in different areas. The construction sequence of landfill site leveling is to clear the slope first, and then level the bottom of the reservoir; the principle of slope leveling is to save earthwork, first remove the surface soil within the scope of the reservoir bottom during leveling, and pile it in the covering soil preparation yard as daily covering soil.
2. Construction Process Flow. Plane compaction of reservoir bottom — 30cm thick pebble groundwater diversion layer — laying filament geotextile (200g / m2) — paving 30cm thick clay layer — paving bentonite cushion 4800G / m2 — 2mm thick HDPE film — joint welding — laying filament geotextile (600g / m2) — 2cm thick medium coarse sand layer — filament geotextile (200g / M2) — 30cm thick pebble leachate diversion layer — filament geotextile 200g / m2 )- primary waste.
3. Quality inspection of HDPE Geosynthetic Membrane Liner and geotextile materials. The anti-seepage membrane and geotextile used in the project are two cloth and one membrane and one cloth and one membrane needling anti-seepage membrane and geotextile. Before use, the laboratory is entrusted to test the technical indexes of the products, and all indexes meet the standard requirements and design requirements.
The impermeable geosynthetic membrane and geotextile have certain anti bursting and anti piercing ability, but in the process of filling garbage, the gravel under the film and the root are often broken. In the anti-seepage construction of the landfill site, the earth excavation shall be removed to the clay layer, and the slope shall be cut and leveled according to the design size, and the underslope shall be backfilled and compacted, leveled and watered for compaction, so that the dry bulk density of the compacted fill shall not be less than 1.65t/m3. The hard sharp objects such as stones and tree roots on the surface shall be removed, and herbicides and other chemicals shall be sprayed. The finished slope surface shall be flat, dense and smooth to prevent the impervious membrane and geotextile from being punctured. After meeting the requirements of design flatness, it is accepted by the supervision engineer to provide working face for the laying of anti-seepage membrane and geotextile.
4. Laying method of HDPE geomembrane and geotextile. The anti-seepage membrane and geotextile are laid at the bottom of the reservoir and laid on the slope. Laying method: the impervious membrane and geotextile are required to be spliced and welded into 20m width on the flat ground, and then laid on the slope surface from top to bottom and perpendicular to the dam axis. After the slope surface is laid and accepted, it is slowly spread from the top of the embankment to the toe of the dike along the direction perpendicular to the embankment axis to connect with the geomembrane at the bottom of the reservoir at the top of the tooth groove at the foot of the slope. After the excavation and acceptance of the bottom of the reservoir is qualified, the bottom of the reservoir shall be slowly paved from the top of the tooth groove to the inside of the reservoir along the direction perpendicular to the axis of the dike foot to the place 25m inside the reservoir.
The laying shall be carried out in dry and warm weather. In order to facilitate splicing and prevent stress concentration, the anti-seepage membrane and geotextile shall be laid in wave form with a margin of about 1.5%. After spreading, the anti-seepage membrane and geotextile shall be leveled and pulled out in time. It is required that the anti-seepage membrane and geotextile shall be consistent with the slope surface without protrusion and wrinkle. The construction personnel shall wear flat bottom cloth shoes or soft rubber shoes, and shall not wear nail shoes to avoid stepping on the geomembrane, If the geomembrane is damaged during construction, it shall be repaired in time.
5. Splicing of HDPE geomembrane and geotextile. The project adopts two cloth and one membrane and one cloth and one membrane for seepage control. The connection of anti-seepage membrane and geotextile is divided into two procedures, i.e. joint of upper layer geotextile and connection of lower layer HDPE membrane. The joint of geotextile is carried out by hand-held sewing machine and nylon thread, the lap width is 10cm; HDPE film is connected by welding process, and the welding tool is double channel plastic heat sealing machine with automatic temperature regulation (speed regulation) electric heating mode. Splicing includes the joint of geotextile and the welding of geosynthetic membrane. In order to ensure the welding quality, welding should be carried out in the factory as far as possible. However, for the convenience of construction, the width of anti-seepage membrane and geotextile should not be too wide, so they must be spliced at the construction site.
The quality of anti-seepage membrane welding is the key to the success or failure of anti-seepage performance. Therefore, the welding of geomembrane must be done well to ensure the welding quality. Therefore, the manufacturer should send professional and technical personnel to the site for operation, guidance and training, and use special welding equipment for geosynthetic membrane. The geomembrane of the project is welded by a professional thermal sealing geomembrane welding machine, and the geotextile is welded by a portable packer.
Welding process: after the first geomembrane is laid, the side to be welded shall be overlapped (about 60cm wide), and the second sheet shall be laid on the first membrane in reverse. The welding edge direction of the two geomembranes shall be adjusted to overlap 10cm.
All welding shall be carried out on site. It is required that the weather is fine and the wind force is below grade 3. It is strictly forbidden to carry out construction in rainy days, high temperature and severe cold weather. The surface of welding base shall be dry. Before welding, the sand, soil and other dirt on the membrane surface shall be blown off with an electric blower, and then cleaned with a clean towel to ensure that the membrane surface is clean. A long board is placed under the welding part to facilitate the welder to walk on the flat base surface Before formal welding, HDPE film of the same material shall be used for trial welding according to the construction temperature and HDPE film thickness. The welding temperature shall be 220-300 ℃, and the welding machine temperature and walking speed shall be mastered, and the construction process parameters shall be determined before formal construction. The weld shall be transparent, smooth, straight and continuous. Two welding seams are spliced, each of which is 10 mm wide. A cavity of 10 mm is reserved between the two welds. The quality of the weld is checked with this cavity.
6. Anchoring of HDPE geosynthetic membrane and geotextile. The anchoring of anti-seepage membrane and geotextile is divided into the anchoring of dam slope and the anchoring of reservoir bottom. The upper anchoring is to embed enough anti-seepage membrane and geotextile at the bottom of the embankment foundation on the top of the dam. Its structural form is rectangular groove, and the filling is rammed in the groove. The trench shall be excavated along the design line of the dam toe. When the anti-seepage membrane and geotextile are laid, the anti-seepage membrane and geotextile shall be close to the inside of the trench, and the filling shall be tamped in the trench.
7. Precautions. In the area close to the level, the formation of bulge is prevented. The bulge will concentrate the gas from the soil under the plastic film layer, so it is necessary to consider the gas discharge outward or at the top. The number of construction joints, especially the horizontal joints on the dam slope, should be reduced as much as possible.
The HDPE geosynthetic membrane shall be protected from perforation during the laying of protective layer. Vehicles and hard soled shoes are strictly prohibited to walk on the HDPE geomembrane liner. Special treatment should be taken at the contact part between the plastic film and the buildings on the top of the dam body and the rigid body under the design water level to avoid leakage and ensure the safety of the landfill area of the refuse plant.
The laying strength of daily construction should be well controlled. The anti-seepage membrane and geotextile laid on the same day must be covered on the same day, and it is not allowed to be exposed for a long time, resulting in material aging.

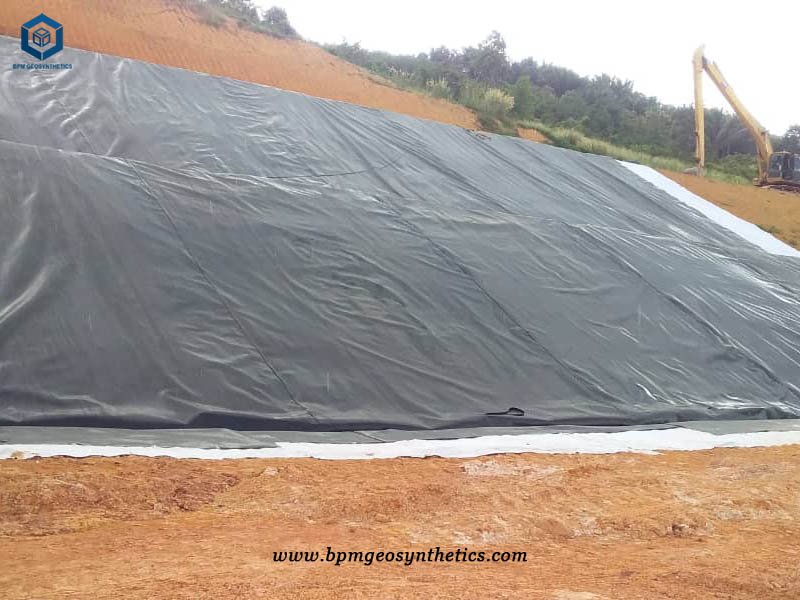
About BPM
BPM has been specializing in delivering one stop geosynthetics products and solutions to worldwide customers since its foundation in 2007. BPM had provided many types of effective and state of the art geomembranes, geotextiles, geocells, geosynthetic clay liners (GCLs), drainage boards, geogrids to over 81countries. Our main customers are from Australia, France, Sweden, UK, Hong Kong, Hungary, New Zealand, Poland, Mexico, Ecuador, Brazil, Pakistan, Bangladesh, Thailand, Vietnam, Malaysia, Indonesia, Singapore, Philippines, Sri Lanka, India, UAE, Saudi Arabia, Qatar, Kenya, Ghana, Ethiopia, Somalia, Nigeria, South Africa, Swaziland, Mongolia etc.
BPM is not only manufacturing best quality geosynthetic products but also providing professional design and installation service. OEM, ODM, custom development and fabrication are also available. If you have any questions or inquiries, please fill and submit the following form, we will reply as soon as possible.